- GMICS
- プラスチック成形
- 生産性向上
- 見える化
- 稼働監視
- 属人化解消
導入から20年以上、時代の変化とともにシステムも更新。GMICSで目指すのは「人に優しい職場」
株式会社セイコーレジン
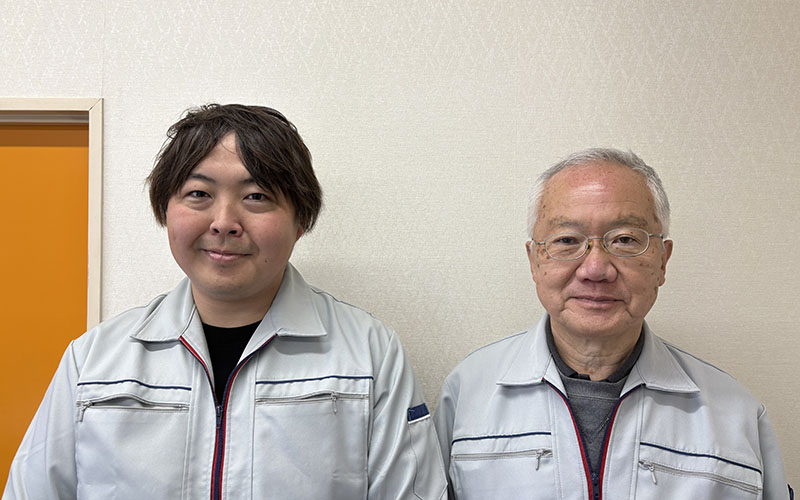
製造部 生産管理 次長 川島様(写真左)
製造部 生産管理 管理グループ 中井様(写真右)
- 業種
- プラスチック成形
- 所在地
- 〒370-0126 群馬県伊勢崎市境下武士661
- 設立
- 1969年
- 従業員数
- 89名(2025年4月現在)
- 事業内容
- プラスチック射出成形・ホットスタンプ・超音波溶着・塗装・組立
- ホームページ
- http://www.seiko-jpn.com/
- 代表者
- 代表取締役社長 天⽥ 誉哉 様
金型の設計・製作から成形・組立まで製造を「一気通貫」「ワンストップ」で対応できることを強みに事業を展開されています。
セイコーレジン様は家電製品、自動販売機部品、自動車等のプラスチック部品の製造、塗装、組立などを行う企業です。グループ会社の株式会社清光金型と連携して製品のデザインや設計、開発、試作、金型製作、成形、塗装、組立まで「一気通貫」「ワンストップ」で担えることを強みに事業を展開されています。
2002年、自社開発の生産管理システムの老朽化に伴い、MICSを導入いただきました。その後、事業の変革とともに生産管理業務の更なる効率化を目的にGrowingMISを導入し、MICSとの連携を開始しました。さらに、2022年には両システムを統合すべくGMICSへ移行しシステムを一本化。「人に優しい職場」を目指してご利用いただいています。
-
導入製品
-
GMICS
-
導入効果
-
まず最初にMICSを導入したことで稼働データの可視化が進み、生産実績・品質記録・稼働状況などをリアルタイムで把握できるようになりました。これにより離れた3工場の状況が24時間、見えるようになりました。
またGrowingMIS、GMICSへと進化させる中で、生産管理業務の自動化・標準化が進み、生産性の向上や属人的な作業の解消につながりました。また成形機の稼働実績などから生産業務の客観的な評価が可能になり、従業員の技術・意欲が向上するといった効果も感じています。
導入前の課題
自社で開発した生産管理システムの老朽化や2000年問題などの課題に直面し、新たなシステムの導入を検討しました。
当初は成形指示が書かれたカードを差立て板に貼り付けるといった手作業で成形計画を立てていたので、週末であっても現場のリーダーが工場に出向き、紙にマス目を作って翌週の計画を立てるといった業務を行っていました。しかし実際の生産状況や急なオーダー変更に応じて都度紙ベースの計画を修正しなければならず、現場の負担が大きくなっていました。そこで1991年に自社で生産管理システムを開発し10年ほど使用していましたが、設備の老朽化や2000年問題などがあり新しいシステムの導入が必要に。そこでタイミングよくムラテックのMICSに出会うことができ、現場目線で作られたシステムであることが決め手となり2002年に導入・運用を開始しました。
解決策と効果
MICS・GrowingMIS・GMICSと時代や環境の変化とともにシステムを更新し様々な課題を改善してきました。
まずは本社工場で運用を開始し、現場の声に耳を傾けながら慎重に導入を進め、2011年には3工場で運用するに至りました。MICSの導入により今まで把握できなかった稼働率や不良率、24時間の成形機稼働状況などのデータが見える化され改善点が明確化したため、リアルタイムに課題を改善できるようになりました。その結果、稼働率が向上し不良率が低減、工場全体の生産効率が改善されました。
その後、時代の変化とともに幅広い製品を製造するようになり顧客数が順調に増加。品目の多様化が進む一方で、生産管理部門の業務負担が大きくなるという課題も生じました。また当時は顧客ごとに担当者が生産を管理しており、各製品の生産状況を担当者しか把握していないという属人化も発生していました。顧客数の増加とともにこのような縦割りの体制では管理が困難になり、業務全体の効率化が求められるようになりました。
そこで2015年に上位の生産管理システムとしてGrowingMISを導入、翌年にはMICSとの連携を開始しました。さらに2022年には、長年のカスタマイズによる機能の煩雑化などを見直す目的で、統合型システムのGMICSへ一本化。これにより自動化・標準化が進み、生産管理の縦割り構造が横断的に。今まで見えなかった担当者の業務が可視化され、属人化が解消されました。今では入社して間もない社員でもGMICSの画面を見ながら業務について議論できるようになり、若手の育成に貢献しています。それだけでなく成形機の稼働実績などを活用することで生産業務の客観的な評価ができ、従業員の技術や意欲の向上にもつながりました。
今後の展開
改善ではなく改革。これからも「人に優しい職場」を目指していきます。
これまでMICS・GrowingMIS・GMICSと、自社の方針や課題解決に最適なシステムを適宜活用してきたことで、生産性の向上や現場力の向上といった改善を進めてきました。しかし今後は業務を「改善」するだけでなく、ムダな工程そのものをなくすといった「改革」が不可欠だと考えています。
究極の目標は「人に優しい職場」をつくることです。成形工場ではどうしても繰り返し作業が多くなりがちです。しかし闇雲に頑張れと言ってその作業にひたすら従事してもらうのにも限界があると考えています。従業員にはもっと自分たちで考え付加価値の高い業務に取り組んでもらいたいと思っています。成形機の稼働状況を見える化したのも、効率の悪さを指摘するためではなく稼働状況を見て従業員が自ら考え自発的に行動することを狙ってのことでした。こうした仕事環境が「人に優しい職場」だと考えています。
その実現のため今後も繰り返し作業のさらなる機械化を推進し、受注から生産・出荷までの工程を完全に自動化することを目指します。すでに受注の取り込み、在庫引当、生産指示、在庫管理、出荷指示、出荷といった業務の自動化をGMICSで実現できており、その結果ルーティンワークが削減され従業員の残業時間も減少しつつあります。
今後もGMICSを活用し業務効率化を進め、生産現場の働き方を改革し「人に優しい職場」の実現を目指します。
導入製品「GMICS」のカタログはこちら