- MICS7
- プラスチック成形
- 生産性向上
- 見える化
- 稼働監視
- 金型管理
- DX推進
成形現場のシステム化にあたり、長年の課題だった複数メーカーの成形機を一元管理できる点が決め手に。
株式会社三琇プレシジョン
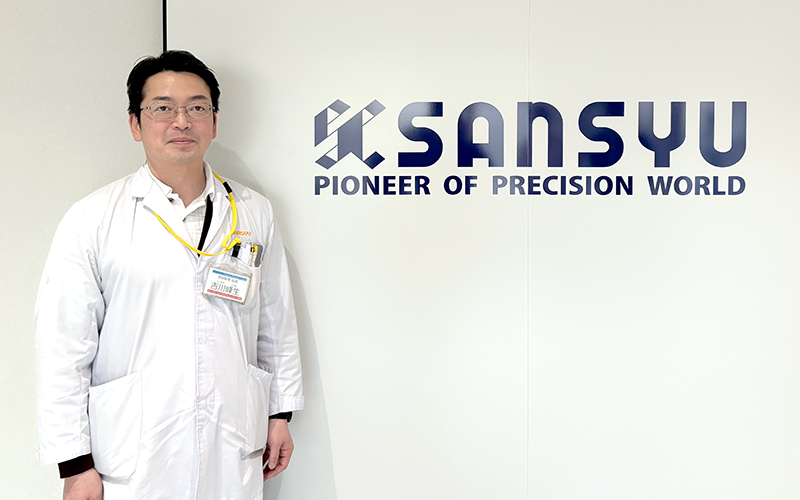
代表取締役社長 岡本様
施設管理 部長 吉川様(写真)
- 業種
- プラスチック成形
- 所在地
- 〒444-1321 愛知県高浜市稗田町四丁目1番地55
- 設立
- 1963年9月
- 従業員数
- 298名(2025年3月現在)
- 事業内容
- 精密プラスチック製品ならびに金属製品の開発製造、販売
- 代表者
- 代表取締役社長 岡本 巌 様
一貫生産体制と高度な精密プラスチック成形技術で高品質なものづくりを実現。「愛知ブランド企業」にも認定され、信頼と実績に裏打ちされた堅実な歩みを重ねる企業です。
三琇プレシジョン様は、精密プラスチック成形分野での確かな技術力と実績を誇る企業です。礎を築いた金属プレス加工からプラスチック成形へと事業を拡大。精密ギアや超小型成形品、2色成形、薄肉成形など多彩な製品をさまざまな業界のお客様に提供されています。
その強みは一貫生産体制と柔軟な生産対応力。金型設計・製作から成形、組立、品質管理まで自社グループで一貫して行うことで、安定した品質を確保しつつ効率的な生産を実現されています。海外にも生産拠点を展開し、金型から設備、材料、生産管理、検査方法まですべて国内工場と同じ環境を実現。オール三琇グループでものづくりに臨まれています。このような卓越した技術力と取り組みが評価され、愛知県内で優れたブランド価値を有する企業に与えられる「愛知ブランド企業」認定を20年以上維持するなど、地域産業を支える存在としてだけでなく、幅広い市場において高く評価される企業として成長を続けておられます。
-
導入製品
-
MICS7
-
導入効果
-
長年にわたり経理は伝票会計、生産管理は各現場ごとにExcelで管理していました。しかし基幹のオフコン運用が難しくなり、新たな基幹システムの導入を検討開始。生産管理も見直し、特に課題となっていた成形機の一元管理を目指しました。検討を重ねた結果、メーカーを問わず成形機と接続できる機能を備え、製造業が開発したシステムであるMICS7を採用することに。
導入後は成形機の稼働状況や生産実績のリアルタイム監視が可能になり、情報の一元化と迅速な判断が可能になりました。また生産計画の調整や金型メンテナンス管理にも活用しており、手作業の削減や業務の効率化を実感しています。
導入前の課題
基幹業務のシステム化にともない、製造現場の課題だった「異なるメーカーの成形機を一元管理」する最適解としてMICS7を選びました。
長年にわたり経理は伝票会計、基幹システムとしてはオフコンを使用していました。しかしオフコンは年々操作できる人が減り、いずれ運用が難しくなるのは時間の問題でした。そこで新たに基幹システムを整備することを決めたのが最初のきっかけです。
せっかくシステムを導入するなら、それまで各現場でExcelなどを使ってローカル管理していた現場管理業務も一括してシステム化しないと根本的な業務改善にはつながりません。そこでまず社内の業務をすべて洗い出し、どのような仕組みが必要かを徹底的に調査しました。その中で浮かび上がった課題の1つが、複数メーカーの成形機の一元管理でした。
この課題を解決するため、さまざまな展示会を回って自社に最適なシステムを探したところ目に留まったのがムラテックのMICS7です。メーカーを問わず成形機と接続できる点に魅力を感じて検討を開始。ムラテックという製造業の会社が開発したシステムという信頼性も決め手となり、成形職場の現場管理を目的に導入を決定しました。
解決策と効果
社内のベクトル合わせに注力して新システムの定着を徹底。課題だった成形機の一元管理に加え、現場の手作業が低減して業務を効率化できました。
導入直後は現場での定着に苦労もありましたが、経営陣が各職場を回り、システム導入の目的や重要性を丁寧に説明し続けた結果、社内理解が徐々に深まりました。現在では現場端末LITへの入力もスムーズに行えるようになりました。
MICS7を導入した最大の効果は、長年の課題であった複数メーカーの成形機の稼働状況をリアルタイムで監視し、生産実績を一元管理できるようになったことです。これにより情報の一元化と迅速な判断が可能になりました。上位システムで立案した生産計画をMICS7に反映させて、現場責任者が成形計画の調整に活用しています。
さらに金型メンテナンス機能も好評です。これまではExcelで個別に管理していた金型のショット数管理をMICS7に移行したことで、規定値に達すると自動でアラート通知されるようになり、メンテナンス業務が格段に効率化されました。このように従来の手作業が大幅に削減され、業務の効率化を実感しています。
今後の展開
システムを有効活用しながら、人が価値を生み出す。次世代へつなぐものづくりと効率的な工場づくりを進めていきます。
これからの時代、製造業においてもシステム化は避けて通れません。デジタル化して終わりではなく、“誰もが迅速に状況を把握し、スムーズに意思決定できる環境”をつくることが必要です。MICS7と上位システム、さらに品質管理システムも含め、生産の見える化、ムダのない工場づくりを目指します。
しかしどれだけシステム化が進んでも、ものづくりの根幹は「人」です。システムは情報整理や自動化を担いますが、最終的な判断や創造力を発揮するのは人間の役割。システムを活用することで、人間が「付加価値を生む仕事」に集中できる環境づくりが重要です。
そのためにも人材育成を最優先課題としています。評価制度を見直し、各職務の評価基準を明確にすることで社員が自身の成長を実感できる環境を整えました。こうした取り組みは海外拠点でも同様で、フィリピンやインドネシア工場でも日本と同じレベルのものづくりができる環境を構築しています。システムと人の力を融合させることで、グローバルで高品質な生産体制を築いていきます。
導入製品「MICS7」のカタログはこちら